Best Practices for Maintaining Your Crawler Dozer’s Undercarriage and Tracks
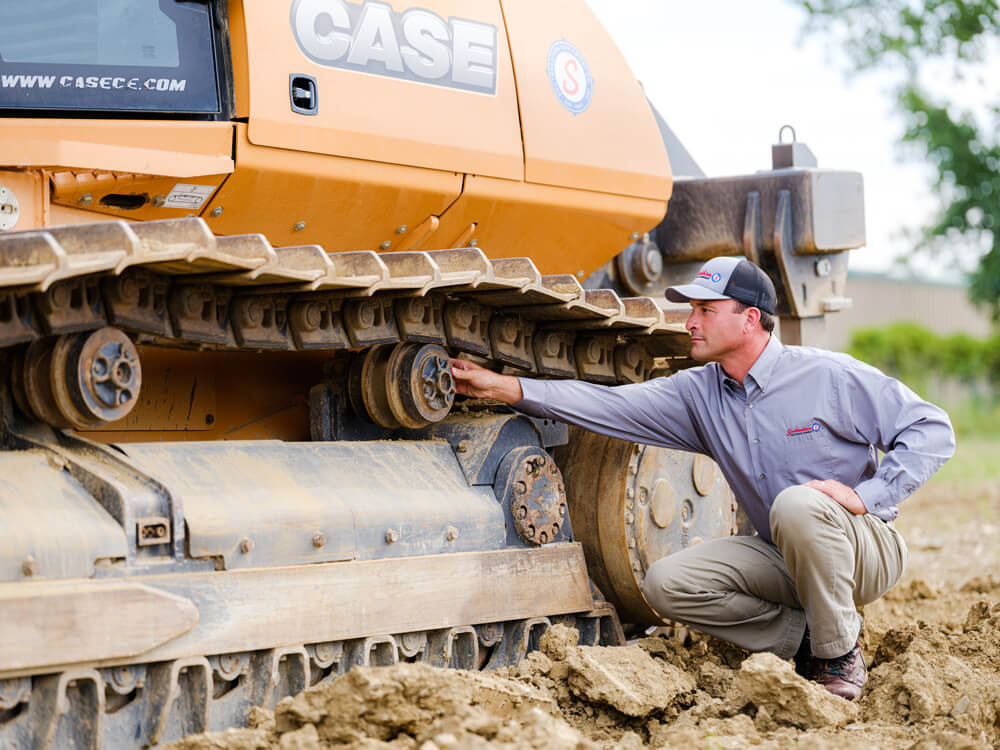
Undercarriage repair is seemingly inevitable, and always expensive: 50% of machine owners’ maintenance costs are spent on machines’ nether regions, so to speak. But such costs can easily be reduced, and even eliminated, with proper undercarriage and track maintenance. To help you along, here are 9 ways to extend the life of your undercarriage and tracks.
- Feel the (Track) Tension: Check your track tension regularly, especially if you work on softer surfaces, such as sand, mud, or snow, that can become compacted in grooves, putting undue tension on tracks and leading to preventable damage. If you work in such conditions, be sure to also hose or otherwise clean your tracks at the end of each shift.
- Tip: To check track tension, hold a straight edge across the track line’s top. Measure the sag between that line and the track’s actual placement. If loose, tighten to your manufacturer’s recommended tension. Failure to do so is asking for an expensive break that’s sure to decommission your machine for at least a few days. CASE offers a kit to help you along.
- Size Matters: Tracks that are too large for your machine not only reduce efficiency, but run the risk of rubbing against or otherwise damaging the undercarriage. Tracks that are too small diminish machine efficiency and add strain to its overall integrity. Keep your machine running well, and reduce costs, by being like Goldilocks: get tracks that are just right.
- Get in Alignment: Misaligned tracks are the greatest contributor to wear on tracks and undercarriages, and not to mention the havoc they can wreak on track links, idler flanges, track and carrier roller flanges, and sprockets. Uphold your alignment by regularly tightening loose tracks.
- Speed Kills: CASE machines are built to last, but going too fast for the job is an almost guaranteed way to wear down your machine, from top to bottom, from undercarriage to engine. Prevent damage and repair costs by keeping your speed within reasonable rates.
- Minimize Impact: Obviously, the worksite can be a harsh environment, and no one’s asking you to go gentle on your machine. But avoid unnecessary roughness to maintain machine integrity.
- Slip Sliding Away: Working on slippery surfaces, such as muddy hillsides, increases wear on all components because the machine has to work harder to get its footing.
- Don’t Play Favorite Sides: Only using one side of the machine when moving material will wear down that area faster than if you alternate between left and right, so switch it up every so often, — for your machine’s — and budget’s — sake.
- Reverse Operation: Our machines can be operated in reverse, and by all means should be when the job requires it. But do so minimally because this contributes to more noticeable wear than front facing operation.
- One final note, on surfaces: Watch out for rocky or highly irregular surfaces, which can lead to bending, breaking, or chipping of undercarriage components. Also, wet silts or clay should be avoided, as you’ll sink like a stone, and sand and sandy mud are abrasive to tracks and can accelerate wear.
These tips are just a start. If you use your machine in extreme conditions, such as salted roads or by barreling over sharp rocks, CASE offers optional track guards and open-center track shoes for even further protection.
Order Track Tension Parts Today: https://southeasternequip.com/locations/