Best Practices for Buying, Operating, and Maintaining Thumb Attachments
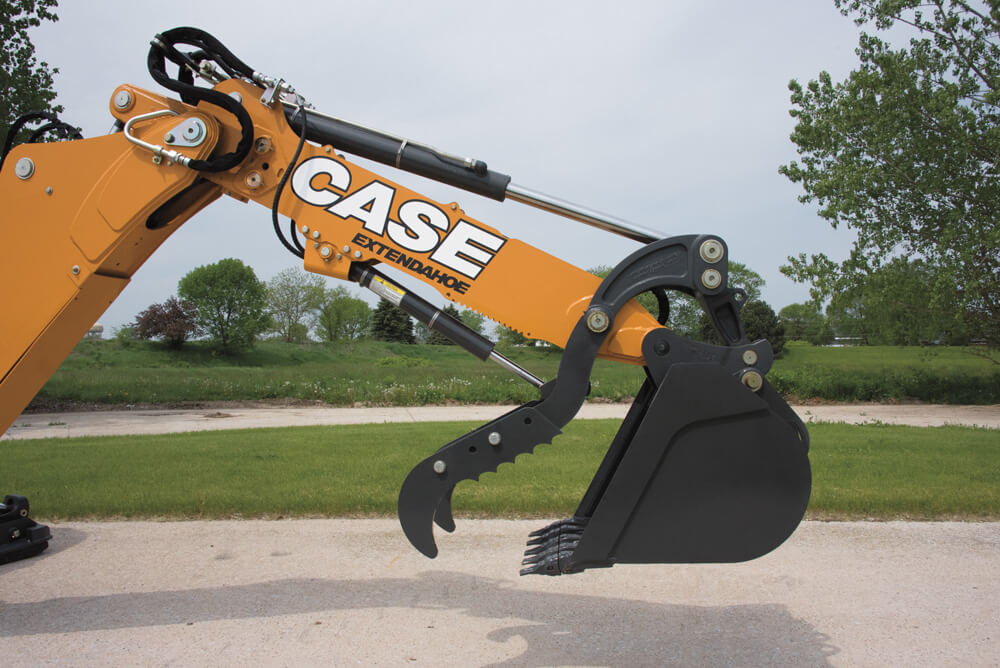
Cost effective, reliable, and efficient, thumb attachments are one of the easiest ways to expand your excavator’s capabilities and performance. Adding a thumb attachment to your excavator instantly opens up new applications, including material handling, land clearing, utility, and road building, all of which can greatly grow your business.
To help you get started, here are best practices for purchasing, operating, and maintaining a thumb attachment for a compact excavator.
Purchasing
Size matters when it comes to buying a thumb excavator, so the first thing you want to do is make sure the thumb matches the bucket. No matter which type of thumb attachment you’re considering, manual or hydraulic, the tines or prongs must align to have the components in sync and guarantee a seamless rotation. Whether you’re buying a manual or hydraulic thumb excavator, confirm you have the right fit for your machine and the use you’re planning.
Operating
As with all heavy equipment, it is essential that users consult the operating manual before actually operating the equipment for the intended use. This step provides an opportunity to confirm lifting capacity and other limitations. The surest way to break a thumb attachment is to overload it, so always keep load levels in mind while operating.
Maintenance
Thumb inspection and maintenance should be part of your daily routine. Any dirt or debris should be cleared from pins and bushings to prevent wear, and thumb teeth should also be inspected for any erosion. Working with dull teeth decreases productivity, increases fuel consumption, and provides unnecessary strain on the attachment.
Also, pins, bushings, and couplers should be greased at the manufacturer’s recommended intervals. Consult your operator’s manual for your specific machine to keep it running smoothly for years to come.